|
PRERADA PLASTIČNIH MASA
Pod preradom plastičnoh masa podrazumevaju se svi postupci kojima se od
polimera (sirovine) dobijaju polufabrikati ili gotovi proizvodi. Postupak
prerade zavisi od sastava, vrste i stanja polimera. Postupci prerade obično
se dele prema tehnologiji prerade, nezavisno od hemijskih i fizičkih promena
koje se dešavaju za vreme prerade.
Postoje dva osnovna postupka: - Prerada bez upotrebe pritiska:
livenje, uronjavanje, premazivanje, impregniranje, sinterovanje .
- Prerada uz upotrebu pritiska i istovremeno dovođenje, odnosno odvođenje
toplote presovanje, livenje pod pritiskom, ekstruzija, valjanje, savijanje,
utiskivanje, duboko izvlačenje . Vrednosti pritisaka i temperatura,
kao i vremena njihovog delovanja zavise od fizičkih
i hemijskih osobina plastične mase (tečljivost, toplotna stabilnost itd.).
Postupci prerade plastičnih masa se mogu podeliti na:
- Osnovne operacije prerade,
- Prerade polufabrikata i
- Pomoćne operacije prerade.
Osnovne operacije prerade plastičnih masa su;
- Kalandrovanje,
- Presovanje (obično, posredno, inekciono),
- Ekstrudiranje (folija, cevi, traka i ploča),
- Ekstruziono brizganje,
- Ekstruziono duvanje šupljih tela,
- Proizvodnja veštačkih pena i
- Prevlačenje metalnih predmeta veštačkim materijama.
2 KALANDROVANJE
Kalandrovanje je slično valjanju metala. Primenjuje se za dobijanje tankih
folija. Suština postupka je u višestrukom propuštanju fabrikata kroz zagrejane
valjke, tako da se debljina stalno smanjuje. Kalandrovanjem se dobija
folija debljine od 0,04 do 3 mm. Postupak kalandrovanja se izvodi pomoću
mašine koja se naziva kalander. Proizvodnja na kalanderu je kontinualna
i koristi se u masovnoj proizvodnji, kada je potrebno proizvoditi velike
količine.
Tri osnovne vrste kalandera su kalanderi za:
- izvlačenje folija,
- peglanje i
- utiskivanje dezena.
Kalander za izvlačenje folija prevodi izmešani
i homogeno plastificirani materijal u tanke folije beskonačne dužine.
Kalander se sastoji od tri, odnosno četiri cilindrična valjka, paralelno
postavljenih sa suprotnim smerom obrtanja. Vruća masa se kontinualano
dodaje između prva dva valjka kalandera, istiskuje u razmak između drugog
i trećeg, a zatim trećeg i
četvrtog,
pri čemu se debljina izjednačava i površina polira. Iza valjka se nalaze
uređaj za hlađenje, merenje, obrezivanje i namotavanje gotovih folija.
Upravljanje procesom proizvodnje folija zahteva usklađivanje različitih
operacija, posebno u pogledu sastava, temperature, brzine, kapaciteta
itd. Na kalanderu se najčešće prerađuju omekšani i tvrdi polivinil hlorid.
Kalander za peglanje se koristi za dobijanje glatkih površina
folija i ploča, dobijenih ekstruzijom. Uređaj se sastoji od 3 paralelno
postavljena valjka sa poliranim površinama. Rastojanje valjaka se precizno
reguliše.
Kalander za dezeniranje utiskivanjem sastoji
se od gravirnog valjka i kontra valjka sa elastičnom površinom (obično
guma ili presovani papir). Dezeniranje utiskivanjem vrši se u plastičnom
stanju. Materijal se odmah hladi da bi se sprečila
deformacija dezena.
Slika 2.1 – Šematski prikaz kalandrovanja
3 PRESOVANJE PLASTIČNIH MASA
Izrada delova od plastičnih masa presovanjem vrši se u alatima (kalupima)
za presovanje, koji imaju jedno ili nekoliko profilisanih udubljenja sa
konturom koja odgovara obliku dela. Udubljenja alate se ispunjavaju plastičnom
masom (u čvrstom ili rastoplenom stanju) i pod dejstvom toplote i pritiska
izvodi se oblikovanje dela.
Osnovni postupci izrade delova od plastičnih masa u alatima za presovanje
su:
-kompresiono presovanje,
-posredno presovanje i
-injekciono presovanje (presovanje brizganjem i livenje pod pritiskom).
Prva dva načina presovanja pretežno se primenjuju kod izrade delova od
termoreaktivnih plastičnih masa (tzv. duroplasta koji se ne mogu topiti),
dok se livenjem pod pritiskom najčešće izrađuju delovi od termoplastičnih
masa (termoplasti).
3.1 Kompresiono presovanje
Kompresiono (obično) presovanje je najprostiji postupak izrade delova
od duroplasta primenom alata i kalupa za presovanje i široko se primenjuje
u praksi.
Proces običnog presovanja se izvodi na hidrauličnoj presi u dvodelnom
alatu i sastoji se iz sledećih faza rada:
-punjenje udubljenja predhodno zagrejanog alata plastičnom masom,
-zatvaranje alata i izvođenja presovanja, pri čemu materijal omekšava
pod dejstvom toplote i pritiska i popunjava udubljenja alata, a zatim
u toku određenog vremena očvršćava,
-otvaranje alata i izbacivanje gotovog dela (otpreska) iz njega.
Udubljenje alata može se puniti zrnastom plastičnom masom ili prethodno
presovanim komadima (tablete, briketi).
Običnim presovanjem mogu se izrađivati delovi svih veličina i svih vrsta
plastičnih masa za presovanje, osim delova sa dubokim otvorima malog prečnika,
kao i delovi sa armaturom male čvrstoće, koja se pod dejstvom pritiska
materijala može deformisati.
3.2 Posredno presovanje
Ovaj način presovanja izvodi se pomoću alata koji imaju odvojenu komoru
za punjenje od udubljenja alata u kome se vrši oblikovanje dela (Slika
3-3.). Proces presovanja se sastoji iz sledećih faza:
-punjenje komore materijalom, koji se u njoj zagreva i omekšava,
-potiskivanje rastopljenog materijala iz komore za punjenje, preko ulivnih
kanala ka gravuri alata, -vraćanje potiskivača, otvaranje alata i izbacivanje
gotovog dela i -zatvaranje alata i izvođenje sledećeg ciklusa.
3.3 Brizganje
Brizganje je sa ekonomskog aspekta najznačajniji postupak prerade termoplasta.
Glavne prednosti ubizgavanja su u uštedi materijala, manjem vremenu izrade
i manjem potrebnom prostoru za proizvodnju. I pored velikih troškova za
nabavku opreme (mašina i alata) ovaj postupak daje velike prednosti kod
serija od samo nekoliko hiljada komada.
Prednosti ovog postupka su:
-tačnost dimenzija i oblika predmeta, kao i veliku mogućnost oblikovanja
predmeta,
-proizvodnost sa čistom i glatkom površinom u bilo kojoj boji,
-široke mogućnosti dorade, obrade i oplemenjivanja površine,
-brza proizvodnja velikih serija,
-velike mogućnosti iskorišćavanja materijala.
Kao
najveća prednost ovog postupka smatra se činjenica da ovi proizvodi po
svojim dimenzijama odgovaraju alatu. Dakle, sve dimenzije se mogu odrediti
tačno. Brizganje je naročito podesno za velike serije i može se u mnogim
slučajevima automatizovati. Da bi termoplast bio pogodan za preradu brizganjem,
on mora da postane tečan pri određenoj temperaturi, da se može brizgati
u alatu delovanjem pritiska i da pri tome ispuni konturu alata. Termoplast
mora da zadrži tečljivost u izvesnom vremenu, a da pri tome ne dođe do
hemijskog raspada, isparavanja, umrežavanja itd.
Slika 3.1 – Šematski prikaz punjenja alata
Mašine za brizganje rade periodično, proces nije kontinualan. Sirovina
iz ulivnog levka se plastifikuje u grjnom cilindru i iz ovog ubizgava
pomoću potisnog uređaja u vidu klipa ili potisnog puža u alat gde se oblikuje.
Rastopina ispunjava šupljinu alata, očvrsne u njemu i najzad se kao gotov
deo izvadi iz alata.
Tok oblikovanja, koji na prvi pogled izgleda vrlo jednostavno, zavisi
od mnogih uslova prerade, koji znatno utiču na konačni rezultat oblikovanog
proizvoda. Vrlo je važno dovesti u sklad termoplast, alat i mašinu da
bi konačni proizvodi imali veliku upotrebnu vrednost. Zato je u nastavku
dat pregled parametara koji utiču na postupak brizganja.
Pritisak brizganja: pritisak ubrizgavanja zavisi od vrste termoplasta,
dimenzija alata i veličini određenih postupkom injekcionog brizganja.
Na potrebni pritisak brizganja utiču dužina i širina alata, debljina dela
i dimenzije ušća. Sa porastom dužine i širine alata raste i pritisak brizganja.
Smanjenje debljine otpreska i preseka ušća dovodi do povećanja potrebnog
pritiska brizganja.
Povećanje temperature termoplasta zahteva veće pritiske brizganja, dok
povišena temperatura alata neznatno smanjuje pritisak brizganja.
Temperatura brizganja: jedan od najvažnijih problema pri brizganju
termoplasta predstavlja jednoliko zagrevanje materijala. Čim je zapremina
cilindra veća, to treba više toplote dovesti masi. Provodljivost toplote
granulata je slaba. Radi toga će materijal koji je bliži zidu cilindra
u jednom trenutku biti pregrejan. Problem je teži što je veći predmet
koji treba brizgati. Kod klipnih mašina za brizganje ovaj problem je naročito
izražen.
Usavršavanjem mašina za brizganje došlo se do mašina sa potisnim pužem.
Okretanjem puža vrši se mešanje granulata, tako da se postiže efekat jednolikog
zagrevanja.
Temperatura se određuje prema vrsti termoplasta, mašini, odnosno puta
tečenja prema debljini zida, kao i prema tome koliko je iskorišćen kapacitet
mašine. Pri istoj temperaturi mase teško tečljiv termoplast očvrsne u
kraćem vremenu hlađenja, nego lako tečljiv. Tečljivost materijala je u
suštini zavisna od temperature mase, pritiska brizganja i temperature
alata.
Tanki zidovi iziskuju višu temperaturu, jer suviše niska temperatura vodi
ka orijentisanim naponima proizvoda. Međutim, treba voditi računa da suviše
visoka temperatura ne dovede do termičkog oštećenja materijala. Veća temperatura
mase utiče na veće skupljanje dela, ali se deformaciona razlika smanjuje,
a mehaničke osobine povećavaju.
Brzina brizganja; brzina brizganja je brzina kojom se kreće pužni klip
napred. Od te brzine zavisi količina mase koja u sekundi izađe iz mlaznice,
odnosno uđe u alat.
Brzina brizganja je funkcija temperature termoplasta, pritiska brizganja
i mase otpreska. Bira se tako da se kalupna šupljina ispuni još pri plastičnom
stanju termoplasta.
Kod proizvoda sa tankim zidovima bira se veća brzina brizganja. Time se
ograničava orijentacija tečenja, a temperatura mase izjednačava. Suviše
velike brzine brizganja mogu negativno uticati na kvalitet, mehaničke
osobine, izgorelost i listanje.
Naknadni pritisak: naknadni pritisak deluje na kraju faze brizganja. Uključuje
se pre kraja potpunog ispunjenja alata da bi se izbegle eventualne netačnosti
pri doziranju. Naknadni pritisak se bira da deo pokaže što manje ulegnuće,
jer u suprotnom bi bio nepotrebno opterećen unutrašnjim naprezanjem.
Naknadni pritisak ima naročitu važnost kod proizvoda sa debelim zidovima.
Vreme delovanja naknadnog pritiska se određuje iskustveno i opravdano
je reći da je vreme trajanja naknadnog pritiska vreme hlađenja ulivnog
sistema.
3.4 Livenje pod pritiskom
Livenje pod pritiskom (injekciono presovanje) je slično posrednom presovanju.
Izvodi se odgovarajućim alatima na specijalnim mašinama za injekciono
presovanje. Primenjuje se uglavnom za presovanje termoplasta, mada su
poslednjih godina razvijene i mašine za injekciono presovanje duroplasta.
Proces injekcionog presovanja (Slika 3-5.) sastoji se od sledećih
faza:
a) materijal za presovanje dozira se u bunker mašine, odakle se posredstvom
uređaja za doziranje dovodi u cilindar koji se zagreva posebnim grejačem,
b) u cilindru se materijal topi i pod pritiskom klipa (ili pužnog valjka)
potiskuje, preko brizgaljke mašine, ulivne čaure i ulivnih kanala u alat,
c) pošto je temperatura alata niža od temperature materijala, već u toku
procesa popunjavanja udubljenja alata dolazi do naglog hlađenja i očvršćavanja
materijala dela. Posle određenog vremena alat se otvara i otpresak izbacuje
iz njega.
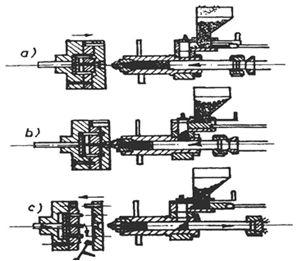
Slika 3.2 – Šema postupka injekcionog presovanja
3.5 Ekstrudiranje
Ekstrudiranje je kontinualan postupak prerade plastičnih masa. Ovim postupkom
plastična masa, kao polazna sirovina, u prahu ili najčešće granulatu ubacuje
se putem levka u cilindar mašine u kojoj je smešten jedan ili više puževa,
koji transportuju, a pod uticajem dovedene toplote prevode je u tečno
stanje. Dejstvom pogona za obrtanje puža, kao i savlađivanjem otpora koji
nastaju transportovanjem rastopljene plastične mase, kroz otvore između
puža i cilindra, masa se plastificira, homogenizira i na kraju u alatu
mašine formira se u željeni oblik. Ova mašina u kojoj se odvija pomenuti
proces zove se ekstruder (Slika 3.3)
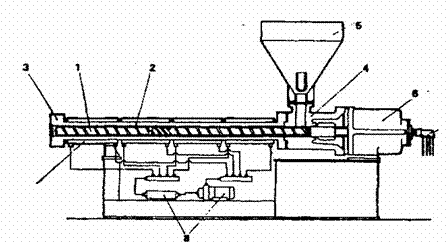
Slika 3.3 – Skica jednopužnog
ekstrudera
1-puž, 2-cilindar,
3-spojnica za spajanje sa alatom,
4-vodeno hlađenje ulazna zona,
5-levak, 6-pogon ekstrudera,
7-temperiranje puža, 8-sistem
za hlađenje i temperiranje cilindra,
9-grejni elementi z agrejanje
cilindra
4 PROCESI EKSTRUZIJE U PROIZVODNJI FINALNIH
PROIZVODA
4.1 Proizvodnja folija i filmova
Proizvodnja
folija i filmova postupkom ekstrudiranja (tehnologija duvanja) Rastopljena
masa ekstrudira se kroz prstenasti alat, formira se crevo određenog prečnika
i debljine zida. Crevo se spolja hladi vazduhom u pravcu kretanja creva,
vrši se stabilizacija dimenzija, čime se sprečava lepljenje folije pri
njenom namotavanju (Slika 4.1).
Slika 4.1 – Ekstrudiranje duvanih folija
4.2 Proizvodnja folija livenjem
Livenje se prvenstveno koristi za proizvodnju folija od termoplasta sa
niskim viskozitetom rastopljene mase (polietilen niske gustine, polipropilen,
poliamid, celulozni acetat i polikarbonat). U ekstruderu pripremljena
masa kroz sito prolazi u široku mlaznicu, nakon čega se u temperiranom
kupatilu (40-50°C) hladi i zatim preko valjaka se cedi voda i film (ili
folija) se upućuju na opkrajanje i namotavanje. Regulacija količine koja
izlazi i debljine folije vrši se pomoću tzv. “usana”. Postoje
tri osnovne konstrukcije mlaznica:
-široka mlaznica sa mogućnošću regulacije obe “usne”,.Široka
mlaznica sa mogućnošću regulacije obe “usne” a-priključak;
b-kućište; c-razdelni kanal; d i d’-ploče, tj. “usne”
koje se mogu regulisati
-samo jedna “usna” je pokretna, a druga je nepokretna, pokretna
“usna” je i fleksibilna, što omogućuje tačno regulisanje razmaka.
Često ovim postupkom dobijene folije, kao na primer u slučaju polistirola,
ne zadovoljavaju uslove u pogledu visokog sjaja. Najbolje rezultate daje
zagrevanje ekstrudirane folije pomoću infracrvenog grejača, postavljenog
između široke mlaznice i kalandera. Prednosti i mane postupka livenja
širokim mlaznicama u odnosu na postupak proizvodnje folija duvanjem su:
Prednosti:
-obezbeđeno je intenzivno hlađenje folija i sprečavanje lepljenja, -omogućena
je kontinuirana kontrola debljine folije, -olakšano je namotavanje folija,
bez nabora, -omogućena je veća produktivnost itd.
Nedostaci:
-maksimalna širina folije ograničena je na 3 m, dok je kod postupka duvanjem
moguće postići širinu do 12 m, -mehaničke osobine folije slabije su od
folija dobijenih postupkom duvanja, -za proizvodnju kesa znatno su pogodnije
folije dobijene duvanjem.
4.3 Oblaganje podloga i proizvodnja laminarnih folija
Ovim postupkom se vrši oplemenjivanje raznih podloga, najčešće papira
u smislu poboljšanja njihovih osobina i postizanja novih osobina: elastičnost,
otpornost na habanje, postojanost prema vodi, mastima i uljima, hemikalijama,
a u specijalnim slučajevima i postizanje nepropustljivosti za gasove i
arome, kao i postizanje estetskog izgleda.
Najraširenija
i najmasovnija tehnika je ekstruziono oblaganje papira i kartona polietilenom.
Postupak se sastoji u plastifikaciji veštačke materije i njenoj ekstruziji,
pomoću široke pljosnate mlaznice .
Slika 4.2 – Oblaganje podloga pomoću ekstrudera sa
širokom mlaznicom
1-ekstruder; 2-široka mlaznica; 3-valjak pritiskač; 4-odmotavanje;
5-hlađenje; 6-namotavanje
4.4 Proizvodnja duvanih šupljih tela ekstrudiranjem
U ekstruderu ili presi za livenje termoplast se zagrevanjem dovodi do
tečnog stanja, a zatim se preko kolenaste glave vertikalno na dole brizga
u obliku creva. Dvodelni otvoreni alat (kalup) obuhvata određenu dužinu
creva, zatvara uz istovremeno uduvavanje vazduha pod pritiskom kroz tanku
cev ili iglu, koja prolazi grlo šupljeg tela. Na ovaj način vazduh pod
pritiskom širi crevo i sabija sa uz hladne zidove kalupa. Nakon hlađenja
alat se otvara i gotov proizvod se vadi iz alata
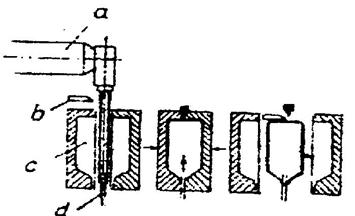
Slika 4.3 – Proizvodnja šupljih tela a-ekstruder; b-nož; c-dvodelni
šuplji kalup; d-ulaz vazduha
Postoje tri mogućnosti za uduvavanje vazduha: aksijalno – odozgo, sa strane
i aksijalno – odozdo
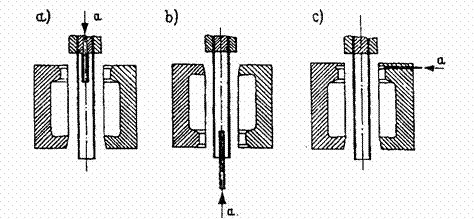
Slika 4.4. – Dovodjenje vazduha a-aksijalno odozgo; b-aksijalno odozdo;
c-sa strane
4.5 Ekstrudiranje vlakana, filamenata i mreža
Za ekstrudiranje vlakana i monofilamenata služe ekstruderi manjih dimenzija,
sa prečnikom puža 30 – 60 mm. Najčešće se ekstrudirana vlakna i filament
naknadno istežu, čime se molekuli posebno orjentišu, te se postiže znatno
veća čvrstoća.
Vlakna i monofilament manjih dimenzija se ekstrudiraju kroz ploču sa više
otvora (10-40). Postrojenje za proizvodnju vlakana i filamenata sastoji
se iz:
-ekstrudera,
-vodenog kupatila,
-uređaja za istezanje i
-uređaja za namotavanje.
4.6 Ekstrudiranje cevi, profila i ploča
Za proizvodnju cevi i profila najčešće se koriste materijali od PVC-a,
polietilena male i velike gustine, polipropilen, ređe poliamid, PMMA,
PC i dr. Kod proizvodnje cevi od PVC-a u prahu, koristi se dvopužni ekstruder,
a od poliolefina i ostalih termoplasta, jednopužni ekstruder.
Istopljena masa iz ekstrudera ulazi u prstenasti alat, iz njega u uređaj
za kalibrisanje, gde dobija predviđenu dimenziju, a zatim u komoru za
hlađenje i uređaj za izvlačenje, i na kraju sečenje
Ekstruzija profila vrši se, u principu, isto kao i ekstruzija cevi.
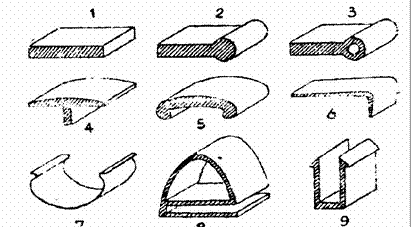
Slika 4.5 – Razne vrste profila
Ekstrudiranje traka i ploča ima praktičnu primenu uglavnom kod omekšanog
i tvrdog PVC-a, modifikovanog polistirola, polietilena male i velike gustine,
polipropilena itd. Pod pojmom trake podrazumeva se “fleksibilna
ploča” debljine 2,5 mm i u principu njena proizvodnja je identična
sa proizvodnjom ploča, izuzev što se trake namotavaju na kalem, a ploče
odlažu na sto za odlaganje.
4.7 Ekstruziono brizganje
Ekstruzionim brizganjem danas se prerađuju svi polimerni materijali:
duroplasti, elastomeri i plastomeri. Od navedenih polimera najrasprostranjenija
je prerada ekstruzionim brizganjem plastomera poznata i pod imenom injekciono
presovanje termoplasta. Zbog toga je u okviru ovog rada ekstruzionom brizganju
posvećena posebna pažnja u narednom poglavlju.
Ekstruziono brizganje se može definisati kao postupak prerade plastomera
brzim ubrizgavanjem plastomernog rastopa u temperiranu kalupnu šupljinu
i ujedno očvršćavanje u željeni oblik proizvoda (često nazvan otpresak).
Glavne prednosti prerade polimernih materijala postupkom ekstruzionog
brizganja su u uštedi materijala, manjem vremenu izrade i manjem potrebnom
prostoru za odvijanje procesa proizvodnje. Najčešće primenjene mašine
za ovu vrstu obrade polimera su ekstruderi sa pužnom predplastifikacijom.
Kroz levak u ulazni otvor cilindra dolazi granulat plastomera. Puž ekstrudera
zahvata granulat i transportuje ga napred ka zagrevanom delu cilindra.
Na tom putu plastomer se pomera, zagreva i prelazi u rastop. Na kraju
puža rastop izlazi pod pritiskom kroz mlaznicu i popunjava kroz ulivni
kanal kalupnu šupljinu. Nakon završetka zapreminskog popunjavanja kalupne
šupljine i kompresije rastopa deluje naknadni pritisak koji služi za kompenzaciju
kontrakcije proizvoda pri hlađenju. Po završenom hlađenju, kalup se otvara
i vrši se izbacivanje gotovog proizvoda.
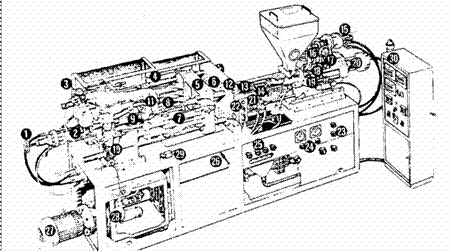
Slika 4.6 – Šematski prikaz ekstrudera sa pužnom predplastifikacijom
1-podešavanje hoda zatvaranja i otvaranja kalupa;2-cilindar za zatvaranje
kalupa;3-automatska pumpa za podmazivanje;4-udešavajuća poluga pumpe za
podmazivanje;5-pomična ploča-strana izbacivanja;6-čvrsta ploča -strana
mlaznice;7-kolenaste poluge-pokretači;8-izbacivačka poluga;9-pokretna
motka;10-uređaj za podešavanje približavanja kalupa;11-komandni uređaj
za otvaranje kalupa;12-mlaznica;13-grejači cilindra;14-puž; 15-hidromotor;16-redukcioni
zupčanici;17-brzinomer;18-glavni zupčanik puža;19-elastična spojka puža;
20-hidraulični cilindar na strani ubrizgavanja;21-povratni cilindar;22-komandna
ploča;23-hidraulični ventil; 24-manometar;25-uređaj za kontrolu vode za
hlađenje;26-elastična balansirajuća komanda za zaustavljanje radnog ciklusa
za slučaj da izostane ispadanje otpreska iz kalupa;27-pogonski motor pumpe;28-pumpa;
29-selektor elektr. zaštite; 30-upravljački i kontrolni uređaj
4.8 Ekstruziono duvanje
Ekstruziono duvanje se može posmatrati kao dvokoračni proces. Prvi korak
obuhvata proizvodnju poluproizvoda ekstrudiranjem, a drugi korak duvanje
u konačni oblik i hlađenje gotovog proizvoda u alatu. Kao poluproizvod
se koristi epruveta dobijena pri stalnoj ekstruziji. U specijalnim slučajevima
su korisnije ekstruzione folije sa širokim razrezom, ili par folija.
Tehnologija proizvodnje šupljih tela tehnikom duvanja je podeljena u dve
velike oblasti. Prva sadrži proizvodnju šupljih tela do 5 l zapremine
ili oko 0,5 kg težine, druga proizvodnju većih i težih tela. Za obe oblasti
poznati procesi omogućuju izradu šupljih tela zapremine između nekoliko
mililitara i 2000 l, odnosno težine između nekoliko grama i 72 kg.
U oblasti do 5 l zapremine koristi se ekstruzija sa izmičućim agregatom
za duvanje (kompresorom), cirkulacionim delom (sa klimajućim ekstruderom),transportom
poluproizvoda ili dvostraničnim sistemom sa pokretnim (povlačenje i izvlačenje)
alatom za duvanje. Koriste se i dvostranični sistemi sa skretnicom. Danas
se najčešće koriste uređaji sa više glava i kompjuterski upravljanjem
trna za uravnoteženje duvnotehnički uslovljene razlike u debljini zida
u pravcu ose i korekture dužine za izjadnačenje debljine zida na obimu,
kod duvnotehnički nepovoljnih preseka. Poluproizvod (crevo) je odvojeno
ili ispod dizne ili kroz sistem za sečenje sa hladnim ili vrelim nožem.
Neophodna brzina noža pri ovom procesu iznosi preko 4 m/s. Na nekim sistemima
transportuju se međusobno lančano povezana šuplja tela.
Uprošćen prikaz procesa dat je na Slici 3-18. Kretanja pokretnih delova
mašine za duvanje, kao i međusobni položaj tih delova se razlikuju od
mašine do mašine, zavisno od njene koncepcije.
Slika 4.7 – Faze procesa duvanja
1-dizna;2-epruveta (čarapa,crevo);3-alat;4-osnovna ploča;5-nož za
sečenje;6-duvaljka;
7-gotov proizvod
Po ekstrudiranju poluproizvoda (faza I) zatvara se alat (faza II) i nožem
se seče poluproizvod (faza III), da bi se zatim alat pomerio ka duvaljci
i duvaljka prišla alatu (faza IV). Nakon duvanja i hlađenja plastike u
alatu, alat se otvara i odvaja gotov proizvod (faza V).
4.9 Proizvodnja veštačkih pena
Veštačke pene sastoje se od velikog broja relativno malih, ovalnih, gasom
ispunjenih ćelija. Međusobno se razlikuju s obzirom na fizičke osobine,
kao što su: specifična težina, tvrdoća, fleksibilnost, propustljivost
gasa i para, upijanje vode, postojanost prema raznim hemijskim agensima,
termoizolaciona i izolaciona svojstva zvuka itd. Od ovih osobina, u najvećoj
meri zavisi oblast primene spomenutih materijala u praksi.
Tri osnovna načina proizvodnje penušavih sintetičkih materijala su:
1) mešanje veštačkih materija sa tečnom penom,
2) naduvavanje fizičkim putem i
3) naduvavanje hemijskim sredstvima.
PVC, polietilen i polistirol su materijali koji se najčešće danas prevode
u penasta stanja ekstruzijom.
4.10 Prevlačenje metalnih predmeta veštačkim materijama
Prevlačenje metalnih i drugih predmeta veštačkim materijama može se vršiti:
-potapanjem u fluidizirani prah veštačkih materija,
-raspršivanjem hladnog praha veštačke materije na predgrejani predmet,
-plamenim raspršivanjem praha pomoću pištolja za metaliziranje,
-raspršivanjem ili nanošenjem tečne disperzije ili rastvora polimera i
-potapanjem u tečnu disperziju.
Površina predmeta koja se oblaže mora da bude ravna, bez rupa ili šupljina
u kojima bi mogao da zaostane vazduh. Ona ne sme da bude masna. Oprema
koja je potrebna za prevlačenje predmeta veštačkim materijama sastoji
se od peći za predgrevanje i rastapanje unutar kojih se nalazi transporter
ili uređaj za vešanje metalnih predmeta. Na njega se nanosi prah veštačke
materije, a u drugoj peći vrši se rastapanje.
Za proces ekstruzije danas se isključivo koriste termoplastične mase.
One mogu da, pod uticajem temperature, pretrpe permanentno deformisanje
bez promene fizičkih i hemijskih osobina. Sposobnost deformisanja oblika,
pod uticajem toplote, i vraćanja u prvobitno stanje je osnovna osobina
termoplastičnih masa.
5 SAVREMENI POSTUPCI PRERADE POLIMERNIH MATERIJALA
5.1 Uvod
Nezaustavljiv tehnički napredak postavio je i pred tehnologije prerade
polimera nove zahteve. Proizvodi s područja informatike, telekomunikacija
i biotehnike ne mogu se zamisliti bez polimernih materijala.
Opseg proizvodnje polimera nesumnjivo mora pratiti stope rasta u svim
sverama proizvodnje. U svetu, tokom 2002. godine proizvedeno oko 155 miliona
tona plastičnih materijala1 (od čega 2,4 miliona tona duromera)2 i 16
miliona tona kaučuka3. U prvih deset godina ovog veka očekuje se porast
potrošnje polimernih materijala uz prosečni godišnji rast od 5,5 %. Očekuje
se da će proizvodnja plastičnih materijala dostići 2010-te godine brojku
od 230 miliona tona, a 2020. 380 miliona tona4. Razlog su tome poboljšani
uslovi života i dalja uspešna zamena drugih vrsta materijala. Današnja
potrošnja plastike u Zapadnoj Europi iznosi 94,8 kg/stanovniku, a 102
kg u SAD . Porast prerade i potrošnje plastike i ostalih polimernih materijala
ima za posledicu razvoj novih i poboljšanje postojećih tehnologija prerade
i porast proizvodnje mašina i prateće opreme.
Suvremene proizvode je nemoguće zamisliti bez polimernih materijala, a
razvoj novih proizvoda, i postavljanje novih zahteva na već postojeće
imaju za posledicu porast potrošnje polimernih materijala, razvoj novih
postupaka prerade i unapređenje postojećih, kao i porast proizvodnje opreme.
5.2 Tankozidno Injekciono Brizganje
Potreba za tankozidnim proizvodima pojavila se paralelno s razvojem uređaja
za mobilnu telekomunikaciju i prenosnih elektronskih uređaja za koja su
zahtevana što lakša i tanja plastična kućišta. Tankozidno injekciono brizganje
(e. thin-wall injection molding) postupak je bez kojeg se danas ne bi
mogla ni zamisliti masovna proizvodnja složenih medicinskih, optičkih,
elektronskih, biotehničkih i automobilskih delova, a posebno različitih
proizvoda i delova mikro veličina6. Smanjivanje, pak, debljine zida otpreska
već je dugo godina i cilj konstruktora injekcionog brizganja delova jer
ono dovodi do uštede materijala i smanjenja troškova proizvodnje7, što
je npr. posebno izraženo u prehrambenoj industriji koja sve više primenjuje
tankozidnu ambalažu. Moguće je reći kako tankozidni delovi (otpresci)
pronalaze primenu na sve više područja i sve više zamenjuju klasične plastomerne
otpreske.
Jedna od čestih primena tankozidnih otpresaka su usmerivači električnih
vodova čija je debljina zida 0,5 mm . Kako bi se otpresak takvih karakteristika
mogao izraditi postupkom injekcionog brizganja, polimerni materijal mora
imati zadovoljavajuća reološka svojstva. Međutim samo to nije dovoljno.
Veliku pažnju treba posvetiti konstrukciji otpreska, konstrukciji kalupa
za injekciono brizganje, i samom postupku injekcionog brizganja.
Postavlja se pitanje gde je granica između tankozidnog i klasičnog injekcionog
brizganja. Otpresci koji pripadaju skupu konvencionalnih ili standardnih,
izrađuju se u polju debljina zida 2,0-3,2 mm. Klasični tankozidni otpresci
imaju debljinu zida 1,2-2,0 mm. Za proizvodnju otpresaka te debljine zida
koriste se standardni polimerni materijali. Otpresci debljine zida manjih
od 1,2 mm pripadaju kategoriji specijalnih tankozidnih otpresaka koji
zahtevaju i specijalne polimerne materijale, preciznije mašine za brizganje
i pažljivije vođenje procesa injekcionog brizganja brizganja. Predviđa
se kako će u bliskoj budućnosti debljina zida većine tankozidnih otpresaka
biti manja od 0,5 mm.
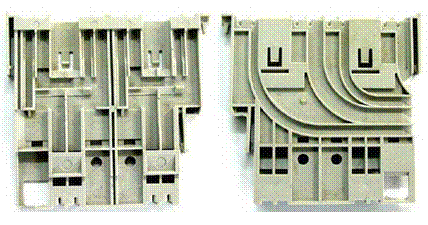
Slika 5.1 - Usmerivači električnih vodova
Postupak injekcionog brizganja tankozidnih plastomernih proizvoda po
pravilu se posebno ne razlikuje od klasičnog postupka injekcionog brizganja
pri kojem se polimerni materijal potrebne smičuće viskoznosti ubrizgava
iz jedinice za pripremu i ubrizgavanje u temperiranu kalupnu šupljinu9.
Ipak, ovaj postupak predstavlja veliki tehnički izazov jer pritisci pri
ovakvoj preradi dostižu i do 150 MPa, a smičuće brzine do 20 000 s . Stoga
se najveće razlike u odnosu na klasične postupke injekcionog brizganja
pronalaze u uslovima prerade, mašinama i alatima.
Potrebno je napomenuti kako smanjivanje debljine zida otpreska nije moguće
bez dodatnog rada na usavršavanju ubrizgavalica i alata. Prednosti koje
ima tankozidno injekciono brizganje kao npr. povećanje proizvodnosti,
smanjenje utroška materijala, brži ciklusi i smanjenje mase otpresaka
opravdavaju dodatna ulaganja.
Debljina zida otpreska i zahtjevi koji se postavljaju na materijal tog
otpreska obrnuto su proporcionalne veličine, što znači što je tanji zid
to su zahtevane vrednosti pojedinih svojstava materijala veće. Materijali
iz grupe plastomera koji se koriste za tankozidno injekciono brizganje
odlikuju se visokim vrednostima udarne radnje loma, čvrstoće, zadovoljavajuće
postojanosti pri povišenoj temperaturi i dimenzione tačnosti. Uz ta svojstva,
bitna su i njihova tehnološka svojstva. Naime, za injekciono brizganje
tankozidnih plastomernih otpresaka karakteristično je usko polje parametara
prerade. Čak i ako su otpresak i alat (kalup) optimirani za tankozidno
brizganje, još uvijek postoje poteškoće pri definisanju parametara. Jedan
od razloga je već spomenuti visoki pritisak ubrizgavanja, zbog čega ubrizgavalice
rade na svojim gornjim granicama. Stoga je kod ovog postupka potrebno
posvetiti posebnu pažnju parametrima prerade, a i samom izboru ubrizgavalica.
Pri konstruisanju kalupa za injekciono brizganje tankozidnih plastomernih
otpresaka potrebno je imati na umu dve važne činjenice. Prvo, pritisak
ubrizgavanja polimerne mase u kalup može biti vrlo visok i drugo, mogu
nastati problemi s izbacivanjem otpreska iz kalupa zbog smanjene krutosti.
Čvrstoća kalupa, sistem za izbacivanje, vrsta i raspored ušća i kanala
za temperiranje, odlučujući su faktori od kojih zavisi vreme ciklusa injekcionog
brizganja. Ne treba napominjati da ušteda od recimo samo jedne sekunde
u seriji od 1.000.000 komada znači uštedu od 1.000.000 s, a to je približno
18 radnih dana s radom u dvije smene.
5.3 Višekomponentno Injekciono Brizganje
Postupak višekomponentnog injekcionog brizganja (e. multi-component injection
molding) razvijen je zbog potrebe da se jedan proizvod izrađuje zbog funkcionalnih
i/ili estetskih razloga od više različitih polimernih materijala i/ili
različitih boja. Njime se prave proizvodi za svakodnevnu upotrebu kao
što su različita pakovanja za potrebe prehrambene industrije, igračke,
delovi kućnih aparata, telekomunikacionih uređaja (slika 2) i niz drugih
konstrukcionih delova kao što su to gumeni ležajevi, prigušnice, elementi
za bravljenje ili klizanje, točkovi i sl.11 Ovim se postupkom izrađuju
npr. poklopci zadnjeg svetla na vozilima čije su komponente različiti
plastomeri i istovremeno su različitih boja.
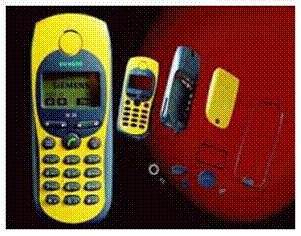
Slika 5.2 - Proizvodi dobijeni višekomponentnim injekcionim brizganjem
Višekomponentnim injekcionim brizganjem moguće je povezati više funkcija
u jednom proizvodu (npr. načiniti proizvode koji istovremeno prigušuju
udare i vibracije i pogodni su za držanje), poboljšati kvalitet proizvoda
i sniziti ukupne proizvodne troškove. Mada ovaj postupak zahteva skuplju
opremu i kalupe, zbog toga što se izbegavaju dodatne operacije, npr. sklapanje
i međuskladištenje delova kao i niz pomoćnih uređaja, isplati se pri velikoserijskoj
proizvodnji.
Do sada je razvijeno nekoliko varijanti višekomponentnog injekcionog brizganja12:
dvokomponentno, trokomponentno, višekomponentno i injekciono brizganje
sa dvostrukom koaksijalnom mlaznicom s iglastim zatvaranjem.
Pri postupku višekomponentnog injekcionog brizganja primenjuje se ubrizgavalica
s dvije ili više jedinica za zagrevanje, a komponente se ubrizgavaju svaka
kroz posebno ušće uzastopno jedna iza druge. Nakon ubrizgavanja prve komponente
u kalup i izrade predoblika, kalup se dovodi u drugi položaj gde mu se
izvlačenjem ili pomeranjem jezgra poveća kalupna šupljina u koju se kroz
drugo ušće ubrizgava druga komponenta. Slika 3 prikazuje dvokomponentnu
ubrizgavalicu u L-izvedbi, a slika 4 moguće položaje jedinica za ubrizgavanje
kod četvorokomponentnih ubrizgavalica.
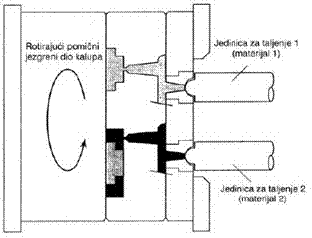
Slika 5.2 - Shematski prikaz dvokomponentnog injekcionog brizganja
s rotirajućim kalupom
Pri izboru materijala treba se pridržavati iskustvenih pravila o međusobnoj
adheziji plastomera, a kako mora doći do toplinske difuzije jednog plastomera
u drugi, poželjno je ubrizgati drugi materijal pri višoj temperaturi taljevine.14
Moguće je povezivanje krutih i savitljivih materijala u jednom otpresku
ili, pak, koristiti kombinaciju više krutih materijala. U višekomponentnom
injekcionom brizganju mogu se kombinovati različiti plastomeri, plastomeri
i elastoplastomeri, plastomeri i elastomeri, kao i plastomeri i silikoni.
Pri izboru kombinacije polimernih materijala treba paziti da s jedne strane
odgovaraju zahtevima proizvoda, a s druge strane mora se, istekom životnog
veka proizvoda, moći što jednostavnije odvojiti kako bi se materijali
mogli reciklirati
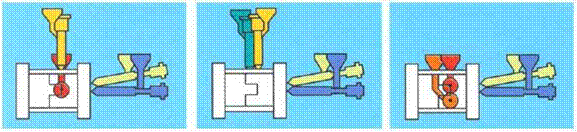
Slika 5.3 - Mogući položaji jedinica za ubrizgavanje kod četvorokomponentnih
ubrizgavalica.
Konstruktori kalupa za višekomponentno injekciono brizganje, s obzirom
na komplikovanost kalupa, moraju biti uključeni u razvoj proizvoda od
samog početka, čime se snižavaju troškovi i skraćuje vreme razvoja. U
zavisnosti od otpreska, kalupi za višekomponentno injekciono brizganje
mogu imati 2-5 kalupnih šupljina i odgovarajući broj ušća. U upotrebi
su rotirajući kalupi, translacioni kalupi, i kalupi sa izvlačenjem jezgra.
Kalupi za višekomponentno injekciono brizganje su, zbog povlačenih ili
kliznih jezgara 70-80 % skuplji od uobičajenih.
5.4 Injeksiono Brizganje Sa Duvanjem
Injekciono brizganje sa duvanjem se koristi za proizvodnju šupljih izradaka.
Često se poistovećuje s postupkom ekstruzionog duvanja, međutim, debljina
zida koju je moguće postići ovim postupkom znatno je veća, dok šuplji
deo otpreska iznosi 30-40 % zapremine otpreska (kod delova načinjenih
duvanjem šupljina zauzima više od 80 % zapremine).19 Ovaj se postupak
često u literaturi označava kraticom GIT (e. gas-assisted injection molding
technology).
Kod injekcionog brizganja sa duvanjem, kao i kod konvencionalnog, rastop
se ubrizgava u kalupnu šupljinu s pomoću pužnog vijka. Rastop započinje
očvršćivati na relativno hladnim zidovima kalupne šupljine, a pre nego
što je kalupna šupljina potpuno ispunjena u kalup se uvodi pod visokim
pritiskom inertni gas (najčešće azot). Gas potiskuje rastaljeni polimer
prema zidovima kalupne šupljine i oblikuje šupljinu unutar otpreska (slika
1). Sve se odvija vrlo brzo, a gas svojim visokim pritiskom, 50-400 bara,
deluje kao naknadni pritisak.
Konstruktori alata moraju vrlo pažljivo konstruisati i proizvod i mlaznicu
kako bi optimizirali smer tečenja gasa. U protivnom će se putanja gasa
usmeriti ka mestima manjeg otpora i prema tanjim delovima otpreska.
Najveća prednost injekcionog brizganja sa duvanjem je mogućnost izrade
otpresaka s kanalima i drugim šupljinama čiji zidovi imaju pojačanu krutost
ali bez povećanja mase otpreska. Na ovaj se način mogu proizvoditi veliki
otpresci, vrlo velikih preseka i različitih zahtevanih debljina pojedinih
zidova. Tu su još i smanjenje proizvodnog ciklusa, smanjenje mase otpreska,
manja ulegnuća na površini izradka, ujednačenije punjenje kalupne šupljine
sa smanjenim naprezanjima, smanjeno vitoperenje optreska itd.22 U zavisnosti
od konstrukcije otpreska uštede na materijalu kreću se i do 50 %.
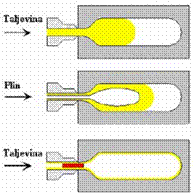
Slika 5.4 - Prikaz injekcionog brizganja sa duvanjem
Pri injekcionom brizganju sa duvanjem gas se uvodi u sredinu kalupne
šupljine i na taj se način postižu šupljine, ili na spoljašnjem zidu otpreska,
potiskujući rastop, i na taj se način izrađuju različiti željeni kanali
na otpresku.
Injekcionim brizganjem sa duvanjem najčešće se proizvode kućišta kućnih
aparata, mašina i televizora, palete za materijal, stolice i stolovi,
ručke, automobilski odbojnici i rezervoari za gorivo, palice za golf i
sl.
Na slici 5.5 prikazana je šuplja ručka načinjena injekcionim brizganjem
sa duvanjem kojim je postignut viši nivo kvaliteta i smanjeni troškovi
u odnosu na konvencionalno rešenje kojim su
izrađivane dve šuplje ljuske delovanjem podpritiska i za
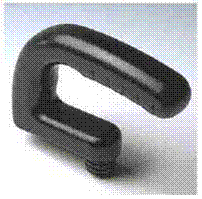
Slika 5.5 -Ručka uredjaja za čišćenje visokim pritiskom
5.5 Injekciono Brizganje Pomoću Vode
Postupak injekcionog brizganja pomoću vode (e. water-assisted injection
molding) gotovo je identičan injekcionom brizganju sa duvanjem, ali se
kao medij za izradu šupljina i kanala koristi voda pod pritiskom od približno
240 bara
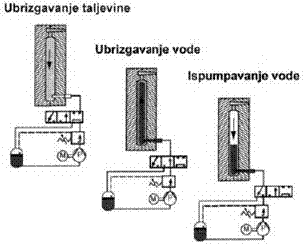
Slika 5.6 - Injekciono brizganje pomoću vode
U odnosu na gas, voda ima neke prednosti. Nije stišljiva, a kako je po
viskoznosti vrlo slična polimernom rastopu, upotrebom vode moguće je oblikovati
šupljine odnosno otpreske sa ujednačenijim i glatkijim zidovima većih
dimenzija. Kako voda ima i bolju toplotnu provodnost i toplotni kapacitet
moguće je skraćenje vremena oblikovanja i ciklusa prerade i do 70 %. Gas
se širi smerom najmanjeg otpora, a voda nastoji zadržati smer ubrizgavanja
te se stoga pomoću vode lakše postiže smeštaj šupljina unutar otpreska.
Nedostaci postupka su zahtevnija izrada opreme koja mora sprečiti prerano
prodiranje vode u kalup što može dovesti do velikog procenta škarta.
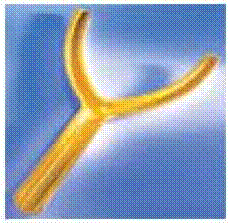
Slika 5.7 - Ručka teniskog reketa načinjena injekcijskim
brizganjem s pomoću vode
Mada je postupak još uvijek u razvojnoj fazi, 1998. zabeležena je njegova
prva komercijalna upotreba. Jedna nemačka firma odlučila je načiniti kolica
za samoposluživanje od tri velika dela načinjena od ojačanog polipropilena.
Prvi izbor je bilo injekciono brizganje sa duvanjem. Međutim, primene
injekcionog brizganja pomoću vode je prevagnulo zbog skraćenja ciklusa
za 70 % (sa 280 s na 68 s) i povećanje proizvodnosti za 3,5 puta. Proizvedena
kolica teže 17 kg što je upola manje od metalnih uz istu čvrstoću.
Slika 5.8 prikazuje Aquamold, Battenfeldov sistem za injekciono brizganje
pomoću vode razvijen u suradnji sa nemačkim IKV-om.
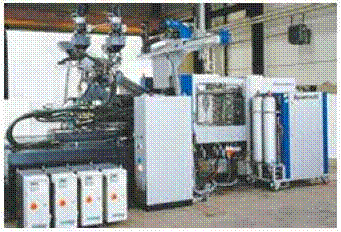
Slika 5.8 - Battenfeldov sistem za injekciono brizganje
pomoću vode
5.6 Koekstrudiranje
Koekstrudiranje (e. coextrusion) je naziv postupka prerade plastičnih
masa pri kojem se kombinuje nekoliko različitih materijala.30 Radi se
o modifikovanom obliku ekstrudiranja, postupku pri kojem se brizganjem
rastopljenog polimera kroz mlaznicu proizvode beskonačni gotovi proizvodi
ili poluproizvodi. Brizgani polimer očvršćuje u ekstrudat. Međutim, kako
najčešće ni jedan polimerni materijal ne može svojim svojstvima zadovoljiti
svim upotrebnim zahtevima koji se postavljaju pred proizvod, često je
nužno proizvesti kompozitne materijale, načinjene od dva ili više materijala.
Tako se proizvode koekstrudiranja filmovi, folije, ploče ili profili sa
2 do 7 slojeva.
Višeslojni filmovi i boce imaju posebno mesto u prehrambenoj industriji.
Prvi sloj dolazi u direktan dodir sa hranom, film mora biti nepropusan
za tečnosti i vazduh, mora štititi proizvod od UV zračenja i preteranog
svetla. To sve se postiže kombinacijom više materijala upravo u postupku
koekstrudiranja.
Kod koekstrudiranja se upotrebljavaju specijalno konstruisani alati kao
nadogradnja ekstruderima kojih treba onoliko koliko ima slojeva u koekstrudiranom
proizvodu. To znači kako je veliki deo već postojeće opreme za izradu
crevnog filma ili različitih profila upotrebljiv i u postupku koestrudiranja.
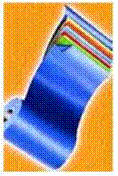
Slika 5.9 - Sedmoslojni koekstrudirani film
za pakovanje
Primena koekstrudiranja smanjuje troškove, podiže proizvodnost i smanjuje
količinu otpada. Naime, ponekad su zahtevana svojstva materijala za određeni
proizvod takva da im ne može udovoljiti jedan polimerni materijal pa čak
ni smesa različitih polimernih materijala ekstrudiranih u jednoslojnom
filmu. Ukoliko su, pak, polimerni materijali nekompatibilni tada ni prevlačenje
nije moguće. Stoga se kombinovanjem nekoliko različitih polimernih slojeva
postižu bolja funkcionalna, zaštitna ili dekorativna svojstva. Razvoj
polimernih materijala, opreme, i potreba za višeslojnim proizvodima rezultirali
su sve većom primenom ovog postupka.
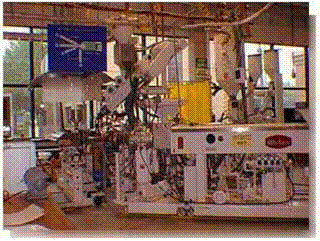
Slika 5.10 - Sedmoslojni koekstruder
Na primer. u Francuskoj su troslojne, ekstruzionim duvanjem načinjene
boce za kratkotrajne prehrambene proizvode gotovo potisnule jednoslojne,
a od 1996. u upotrebi su i šestoslojne. Ove su se boce pokazale izuzetno
dobrim za očuvanje kvaliteta prehrambenih proizvoda.
5.7 Pultrudiranje
Pultrudiranje (e. pultrusion) je kontinualni postupak proizvodnje kompozitnih
profila konstantnog poprečnog preseka. Radi se o postupku prerade kompozitnih
materijala sa izuzetno niskim troškovima koji se sve više primenjuje na
području mašinogradnje, brodogadnje i građevinarstva, uz godišnju stopu
rasta od oko 20 %.37
Linija za pultrudiranje sastoji se od sistema za rukovanje sa namotajima
vlakana, uređaja za natapanje vlakana smolom, naprave za predoblikovanje
profila, alata za zagrevanje, sistema za izvlačenje i rezanje.
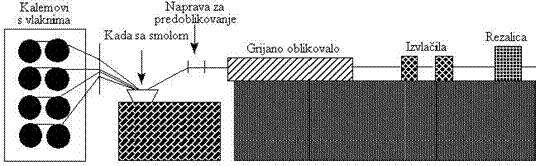
Slika 5.11 - Šematski prikaz linije za pultrudiranje
Proces započinje odmotavanjem vlakana s kalemova i vođenja prema kadi
za njihovo natapanje smolom. Na tom putu vlakna natopljena smolom prolazi
kroz napravu za predoblikovanje u kojoj se ona raspoređuju na željeni
način. Tako oblikovani profil prolazi kroz zagrejavani čelični alat, oblika
željenog proizvoda. Tokom prolaska profila kroz alat započinju polireakcija
i umreživanje što ima za rezultat očvršćivanje ojačane duromerne smole.
Naposletku, ojačani i umreženi profil, konačnih dimenzija i definisanog
poprečnog preseka izlazi iz alata. Kontinuirano kretanje tokom procesa
omogućuje sistem za izvlačenje. Nakon toga profili se režu na željenu
dužinu pomoću automatizovane pokretne testere.
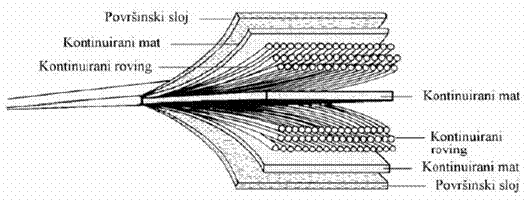
Slika 5.12 - Šema pultrudiranog profila
Jedna od glavnih prednosti pultrudiranih profila mogućnost je prilagođavanja
njihovih svojstava zahtevima kupca i to na sledeće načine: -menjanjem
vrste i sastava smole, a uobičajeno se koristi epoksidna smola (EP), nezasićeni
poliesteri (UP) i vinil-esterska smola, i -menjanjem vrste, udela i rasporeda
vlakana u profilu pri čemu se najčešće upotrebljavaju staklena vlakna
i to E i S staklo i ugljena vlakna. Time se postižu:
-izuzetna koroziona postojanost prema delovanju raznih agresivnih
medija i atmosferilija,
-visoka čvrstoća i žilavost,
-niski troškovi održavanja (ukoliko je održavanje uopšte potrebno),
-jednostavna montaža,
-niska gustoća (povezano s time i masa, niski troškovi transporta i olakšano
rukovanje i manipulacija),
-izuzetna električka i toplotno-izolaciona svojstva,
-nemagnetičnost, i
-postojanost pri povišenim temperaturama.
Pultrudirani kompozitni profili primenjuju se u:
-građevinarstvu (membrane, štitnici kablova, delovi rashladnih tornjeva,
razne rešetkaste konstrukcije, rešetkasti podovi i platforme, nosači,
stepeništa, fasadne ploče, vatrootporna vrata),
-automobilima (lisnate opruge za srednje teška i teška vozila, delovi
autobusa, kočione obloge),
-u širokoj potrošnji (lestve, delovi rasvetnih stubova),
-u postrojenjima za pročišćavanje otpadnih voda (delovi pročistača, delovi
kanala),
-u elektroindustriji (nosači električnih vodova, razni delovi elektromotora,
stubići električnih ograda, antene), itd.
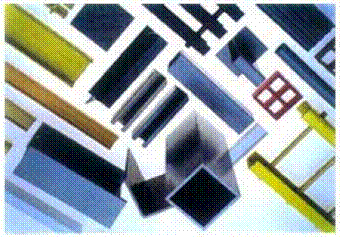
Slika 5.13 - Primeri pultrudiranih profila
5.8 Namotavanje
Namotavanje (e. filament winding) je delimično automatizovani postupak
proizvodnje šupljih, relativno tankih, ojačanih kompozitnih predmeta.42
Većina proizvoda cilindričnog je oblika poput cevi, no mogući su i drugi
oblici, npr. rezervoari i različite posude pod pritiskom. Na ovaj se način
izrađuju krila aviona i štapovi za golf. Unutrašnja površina ovih predmeta
je glatka dok je spoljašnja hrapava.
Najvažniji korak tokom procesa namotavanja je uranjanje vlakana u polimernu
matricu i namotavanje oko rotirajućeg trna. Očvršćavanje se obično vrši
pri povišenoj temperaturi u posebnoj peći ili pomoću infracrvenih grejača
bez delovanja vazduha. Trn se uklanja nakon završenog ciklusa očvršćavanja
ili se ostavlja kao unutrašnja obloga proizvoda.
Vlakna mogu biti u obliku rovinga, vrpci ili monofilamenta koji su impregnirani
smolom u koju je dodano ubrzavalo neposredno pre namotavanja na trn pa
se u tom slučaju radi o tzv. mokrom namotavanju. U postupku suvog namotavanja
vlakna su predimpregnirana, a dobiveni proizvod se često koristi kao predoblik
u postupku injekcionog brizganja smola (e. resin transfer molding, RTM).
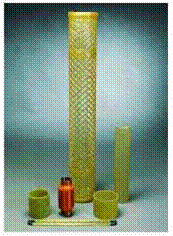
Slika 5.14 - Proizvodi načinjeni postupkom namotavanja
Oprema za namotavanje može se kontrolisati pomoću računara, a izrađuju
se mašine sa 2 do 12 osa okretanja. Troškovi postupka namotavanja vrlo
su niski, a mogu se izrađivati proizvodi u malim i velikim serijama. Većina
prerađivača u ovu svrhu nabavlja standardne polimerne materijale koje
je katkada potrebno malo modificirati, dok drugi pak razvijaju vlastite.
5.9 Ekstrudiranje Mikrocelularnih Pena
Kako na važnosti sve više dobivaju što laganiji proizvodi dobrih mehaničkih
svojstava razvijaju se različiti postupci za izradu penastih proizvoda,
a jedan od njih je ekstrudiranje mikrocelularnih pena. Vođenje procesa
ekstrudiranja mikrocelularnih pena od kristalnih plastomera, poput polipropilena
(PP), znatno je teže u odnosu na ekstrudiranje pena od amorfnih plastomera.
S jedne strane je topivost CO2 u PP-u manja nego u polistirenu (PS).
Stoga su za postizanje homogenog rastopa potrebni viši pritisci tokom
prerade. S druge strane sa sniženjem temperature rastopa se povećava topivost
pene. Da bi se zadovoljila oba uslova, mešavina rastopa i pene homogenizira
se i hladi u statičkoj mešalici. Za regulaciju potrebnog protoka rastopa
i pritiska pridodata je na svaku stranu statičke mešalice po jedna pumpa
(slika 1). Pri tome je drugom pumpom određen protok i pritisak rastopa
u alatu, čime je omogućeno postizanje pritisaka i do 500 bara.
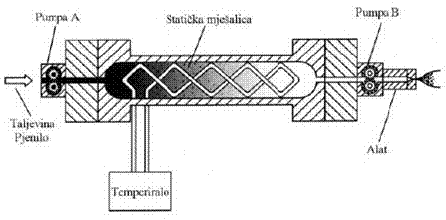
Slika 5.15 - Ekstrudiranje mikrocelularnih pena
5.10 Brizganje Na Poleđinu Pripremka Načinjenog Od
Komadića Prirodne Ili Umetne Kože
Postupak direktnog brizganja staklenih vlakana na poleđinu dekorativne
folije, tekstila ili ručno lepljenu kožu na prethodno pripremljenu podlogu,
već je uobičajeni postupak prerade posebno u automobilskoj industriji.50
Kako bi se izbeglo ručno lepljenje kože na podlogu razvijen je postupak
direktnog brizganja na poleđinu pripremka načinjenog od komadića prirodne
ili veštačke kože. Od ostataka kože prvo se izrađuje folija koja po izgledu,
mirisu liči na kožu. Pripremak se razapinje u okvir prese i na njega se
direktno presuje polimerni rastop ojačan dugim staklenim vlaknima.
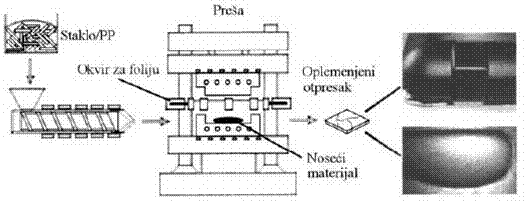
Slika 5.16 - Brizganje na poledjinu pripremka od prirodne ili veštačke
kože
5.11 Lowari Postupak
Sendvič elementi za konstrukcione elemente mogu se izrađivati različitim
postupcima prerade.
U poslednje vreme posebna se pažnja posvećuje smanjenju utroška smole
i punila (ojačala). Jedan od takvih postupaka je LoWaRi postupak. Najznačajnija
novost kod tog postupka je primena trodelnog kalupa umesto do sada uobičajeno
primenjivane vakuum folije. Potrebni gornji i donji deo kalupa pri tome
se mogu s pomoću creva pod pritiskom pomerati u odnosu na postavljenu
ispunu u kalupnoj šupljini. S pomoću vakuum pumpe odzračuje se kalupna
šupljina i ispuna, te se ubrizgava potrebna količina smole. Po završetku
ubrizgavanja spušta se gornja polovina kalupa i smolom se ravnomerno natapa
ispuna. Nakon završenog umrežavanja proizvod se vadi iz kalupa. Ovim postupkom
je moguće izrađivati ojačane ravne ili zakrivljene proizvode s obostranom
visokokvalitetnom površinom. Postupak je pogodan za male i srednje serije.
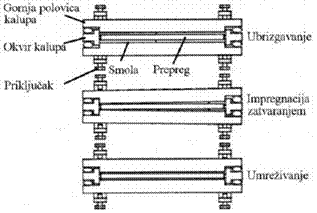
Slika 5.17 - LoWaRi postupak
LITERATURA
Tehnologije Prerade Plastičnih Masa - Bogdan Nedić
An analysis of plastics consumption and recovery in Europe, APME, Brussel.
World plastics supply 2002 – 2010,
Rubber and rubber products Rev,
Forecast for the World Plastics Industry to 2020, Plastics Engineering
Global business trends, partners, hot products, Plastic data source,
Thin-Wall Injection Molding Processes
Thin-wall Technology in the Mobile Phone Industry, KU-Marketing, Informationssysteme,
Leverkusen, 1997
Internet:
http://www.mfkg.kg.ac.rs/index2.php?option=com_docman&task=doc_view&gid=991&Itemid=27
http://www.pardos.marketing.free.fr/24.html
http://www.plasticsdatasource.org/global.html,
http://www.pec.engr.wisc.edu/research/research_008.html,
PROCITAJ
/ PREUZMI I DRUGE SEMINARSKE RADOVE IZ OBLASTI:
|
|
preuzmi
seminarski rad u wordu » » »

Besplatni Seminarski Radovi
|
|